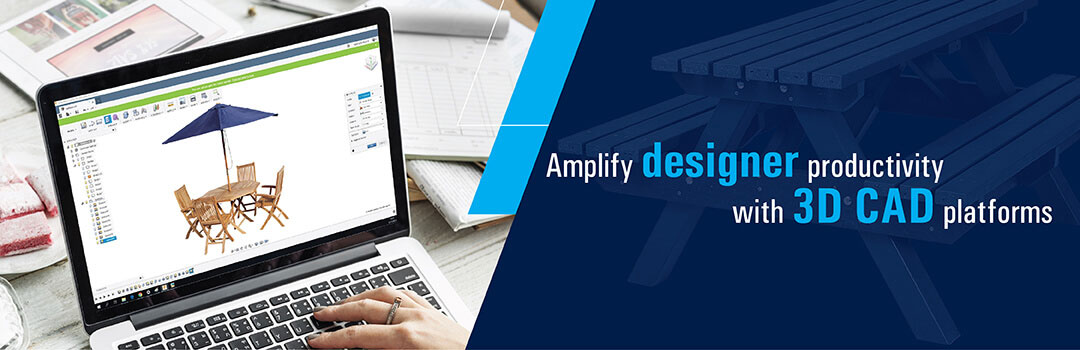
3D design platforms make outdoor furniture manufacturing seamless by facilitating accurate visualizations, lowering prototyping costs, and expediting design iterations. These platforms help manufacturers test dimensions, colours and materials, which enables quick decision making, enhances production workflows, and improves overall efficiency.
Table of Contents
- Importance of Outdoor Furniture Productivity in Competitive Markets
- What are 3D Design Platforms and how they Work?
- Challenges Faced by Outdoor Furniture Manufacturers without 3D Design
- How 3D Design Platforms Enhance Productivity for Outdoor Furniture Manufacturers
- The Role of 3D Design Outsourcing in Enhancing Productivity
- Benefits of Outsourcing 3D Design Services
- Conclusion
- FAQs
Outdoor furniture manufacturers face pressure to deliver innovative and high-quality products quickly and efficiently. Traditional design processes often involve time-consuming prototyping and revisions.
3D design platforms offer a solution for quick and efficient furniture modelling by streamlining the entire design process. Designers can use these platforms to create, visualize, and modify furniture concepts digitally, eliminating the need for physical mock-ups and reducing lead times. This allows manufacturers to respond faster to market trends and customer demands, ultimately increasing productivity and competitiveness.
The global outdoor furniture market was valued at USD 50.73 billion in 2023 and is expected to increase from USD 53.27 billion in 2024 to USD 81.44 billion by 2032.
Source: Fortune Business InsightsImportance of Outdoor Furniture Productivity in Competitive Markets
In a competitive outdoor furniture market, productivity is vital to maintaining profitability and market share. Greater productivity supports manufacturers to lower production costs, improve product quality and condense lead times. This efficiency drives quick innovation, reacts better to client needs, and sustains competitive pricing. This strengthens brand profitability and position.
What are 3D Design Platforms and how they Work?
3D design platforms like SolidWorks and Inventor help 3D modeling services to create precise digital models, drafting and drawings. These 3D modeling solutions utilize CAD principles for accurate object representation, incorporating dimensions and facilitating seamless design workflows through simulations, and integration with manufacturing processes.
Challenges Faced by Outdoor Furniture Manufacturers without 3D Design
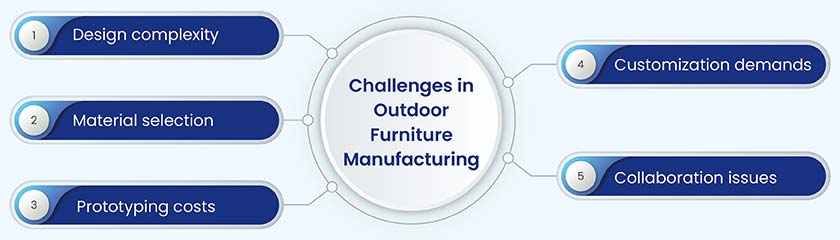
Common Production Bottlenecks: Design Iterations, Material Selection, and Prototyping
- Frequent Design Iterations: Need continuous modifications and cause delays, leading to extended production timelines.
- Material Selection: Leads to challenges that are caused by requirements based on durability, weather-resistance, aesthetic and functional needs.
- Legacy Prototyping: Can be resource intensive, incur higher costs, and extend lead times that impede product development.
- Customization Demands: Consumers increasingly seek personalized outdoor furniture options. Meeting these customization demands can be challenging without efficient design tools that allow for quick adjustments.
- Collaboration Issues: Collaboration between designers, engineers, and manufacturers can be hindered by communication gaps and the limitations of traditional design methods.
The Impact of Inefficiencies on Time-to-Market and Profit Margins
Inefficiencies within production, including extended design adjustments, material delays, and expensive prototyping, diminish competitive advantage and extend time to market. These delays increase operational costs, drop profit margins, and limit the manufacturerโs ability to respond to market demands.
Need for Innovative Solutions to Streamline Operations
Streamlining operations for outdoor furniture manufacturers requires innovative workflows or tools that lower design cycles, optimize material selection, cut production delays, and lower prototyping costs. Integrating advanced automation and technology augments efficiency, lowers production delays and enhances market competition.
How 3D Design Platforms Enhance Productivity for Outdoor Furniture Manufacturers
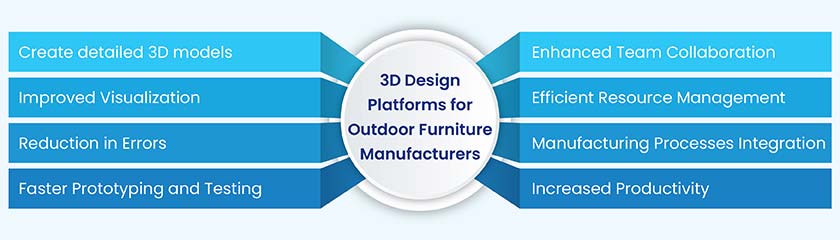
Improved Visualization and Design Accuracy
The Benefits of Creating Detailed 3D Models for Design Clarity
Creating detailed 3D models provides design clarity, enabling precise visualization and analysis of complex outdoor furniture designs. Software like SolidWorks and Inventor allow manufacturers to simulate real-world conditions, identify potential issues early on, and optimize designs for aesthetics, ergonomics, and structural integrity. This clarity minimizes costly errors and rework, ultimately boosting productivity.
Reduction in Errors and Revisions through Accurate Representations
Precise 3D representations for outdoor furniture manufacturing lower revisions and errors by providing accurate visualizations of designs, dimensions and materials. This reduces ambiguities between the concept and the final product, ensuring greater alignment with specifications, mitigates mistakes, and speeds up production cycles.
Faster Prototyping and Testing
How 3D Printing Integrates with Design Platforms for Quick Prototyping
3D printing integrates with design tools to achieve quick prototyping that allows manufacturers to convert digital models into physical prototypes. These workflows expedite testing, iterations and refinement, lowering lead times and costs and enhancing design accuracy before full-scale production.
Speeding Up Testing Processes and Iterative Feedback
Faster testing and prototyping enable manufacturers to accelerate design validation by creating functional models. Iterative feedback reduces testing time and drives rapid adjustments. This process improves product development, lowers errors, and cuts down time-to-market, which improves overall production efficiency.
Enhanced Collaboration among Teams
Facilitating Communication between Designers, Engineers and Manufacturers
Enhanced collaboration platforms enable seamless communication between designers, engineers and manufacturers that ensures alignment for the entire production process. Real-time data sharing and integrated tools support quick decision-making, mitigate errors, and make workflows seamless, leading to improvements in efficiency and product quality.
Tools for Real-Time Feedback and Adjustments
Tools for real-time adjustments and feedback, like cloud-based collaboration platforms and integrated design software, drive seamless communication between teams. These platforms enable instant update sharing, faster revisions, and collaborative problem-solving that ensure expedited decision-making and effective design changes.
Efficient Resource Management
Optimizing Material Usage through Accurate 3D Models
Accurate and data-rich 3D models improve material use by precisely calculating dimensions and lowering material waste during production. These 3D models help manufacturers visualize design components, refine material needs, and simulate material capabilities that ensure efficient resource utilization, cost cutting, and sustainability enhancements.
Reducing Waste and Costs with Better Planning
Efficient resource management includes optimized material use and production workflows to reduce waste and lower costs. By implementing advanced planning platforms, manufacturers can precisely forecast material needs, streamline inventory, and prevent overproduction, which leads to cost savings and a lower environmental impact.
Integration with Manufacturing Processes
Seamless Integration of 3D Designs into CNC Machines and Production Lines
Seamless integration of 3D designs into CNC machines and production lines enables the direct conversion of digital models into accurate physical layouts. CAD/CAM software interfaces improve machine settings, ensure precise cuts, enhance material efficiency, reduce errors, and boost automation and production scalability.
Additionally, using plugins and macros to automate tasks within CAD platforms allows manufacturers to streamline repetitive processes, such as generating patterns, dimensioning, creating part families and producing BOMs (Bill of Materials). Automated flat pattern creation, DXF generation, and documentation also accelerate preparation for manufacturing and sales, further optimizing workflows and reducing manual interventions.
Using plugins and macros, you can automate tasks such as:
- Pattern generation
- Mirroring, dimensioning, and drafting
- Part family creation
- BOM generation
- Flat pattern creation
- DXF files and documentation for manufacturing and sales
DriveWorks Configurator for Enhanced Sales Information Management
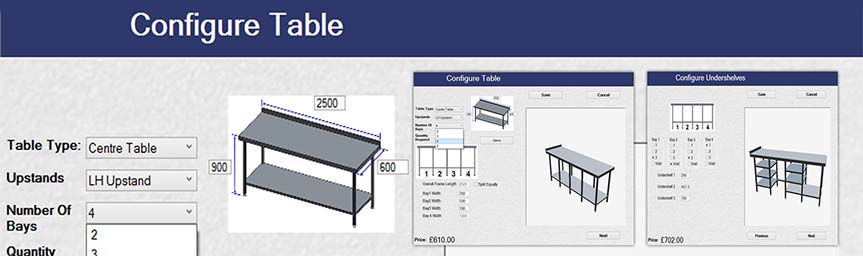
Hitech streamlined custom stainless-steel furniture manufacturing for a US-based manufacturer by implementing an online Configurator with DriveWorks Live. This solution automated design customization and sales, enhancing the customer experience, reducing response times, ensuring secure data access, and eliminating third-party dependencies. The use of DriveWorks Live significantly improved operational efficiency, allowing for faster and more accurate customization of products while keeping processes seamless and fully integrated.
Read Case Study →Streamlining the Transition from Design to Manufacturing
Streamlining the transition from design to manufacturing requires integrating CAD software with 3D printers and CNC machines. This enables the direct conversion of 3D digital models into accurate production specifications, improving accuracy, accelerating workflows, and reducing errors by eliminating manual data transfer and rework.
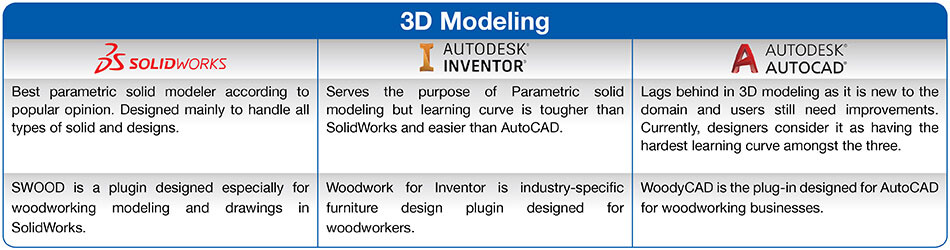
Current market projections show that the global 3D CAD software market is set for significant growth, increasing from USD 11.77 billion in 2023 to USD 20.22 billion by 2031.
Source: SkyquesttThe Role of 3D Design Outsourcing in Enhancing Productivity
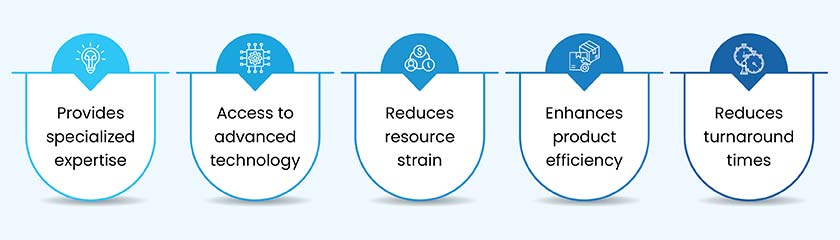
3D design outsourcing plays an important role in improving the productivity of outdoor furniture manufacturers. Using specialized expertise and cutting-edge technology, outsourcing design tasks to third-party professionals allows manufacturers to quickly iterate complex designs, get access to advanced CAD software, and leverage specialized material intelligence.
It lowers in-house resource strain and expedites prototyping, which enables quick turnaround times (TAT). Outsourcing supports manufacturersโ focus on core competencies like logistics and production that ensures high quality and optimized designs. Moreover, third-party design teams can perform simulations and virtual testing, lowering errors, minimizing prototype expenses and improving product efficiency.
For creating best 3D designs of outdoor furniture, design engineers must have knowledge in:
- Design Theory: Focuses on ergonomics, comfort, and space for user-centered designs.
- Evolution of Furniture Design: Traces style history and trends influencing today’s designs.
- Design Application: Uses adaptable methods and flexible techniques for efficient creation.
- Material Research: Prioritizes cost, durability, and eco-friendliness in material selection.
- Fabrication Technologies: Covers cutting, forming, and assembly processes for production.
- Maintenance Essentials: Ensures durability, weather resistance, and options for recycling.
- Communication and Collaboration: Enhances teamwork and client interactions for effective results.
Extremis, a Belgium-based outdoor furniture manufacturer, enhanced efficiency across its entire value chain by utilizing SOLIDWORKS. The software allowed for material integration and precise adjustments to measurements, saving both time and cost. From design and blueprints to marketing and production, SOLIDWORKS facilitated improved collaboration and productivity throughout the companyโs end-to-end manufacturing process.
Source: SolidWorksBenefits of Outsourcing 3D Design Services
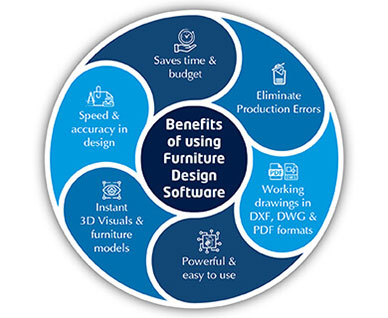
Access to Specialized Skills and Technologies
Outsourcing 3D design services, including furniture CAD drawings, provides access to specialized skills and advanced tools. These platforms enhance productivity by delivering expert design solutions, reducing prototyping costs, and improving material selection. With quick design iterations and high-quality visualization, manufacturers can speed up production, improve product quality, and stay competitive.
Cost-Effectiveness: Focusing Internal Resources on Core Activities
It improves cost efficiency for outdoor furniture manufacturers as it eliminates the need for in-house CAD experts and expensive software. It also supports firms in reallocating internal resources toward core strategic functions and production, utilizing specialized services to improve product development cycles, increase precision, and speedup market entry.
Scalability in Managing Design Projects
Scalability in managing design projects helps manufacturers effectively handle greater volume and complexity. Advanced design platforms provide streamlined adaptation to larger teams, more intricate designs, and varied product lines. Scalable solutions lead to consistent quality, quick turnaround times, and resource optimization that support growth without compromising project results.
Conclusion
In conclusion, 3D design platforms are transformative for outdoor furniture manufacturers, as they drive operational efficiency. Enabling accurate visualization, seamless collaboration, quick prototyping and resource optimization helps streamline production workflows and reduces time-to-market. As manufacturers use advanced 3D design and automation, they can meet market demands for sustainable, durable and high-quality outdoor furniture. Embracing these technologies improves productivity and lowers costs, allowing manufacturers to thrive in a competitive market for innovative and customer-centric products.
FAQs
3D design platforms streamline workflows by reducing prototyping costs, accelerating design iterations and enhancing design accuracy. They enable quick virtual testing of materials, colors and dimensions, allowing faster decision making. This reduces lead times, optimizes resource use and enhances productivity.
3D modeling provides realistic visualizations, reducing errors and revisions by aligning the concept with the final product. It enables precise measurements and detailed simulations, thereby improving design accuracy. This result in faster prototyping reduced waste and higher-quality products.
Yes, 3D printing can be directly integrated with 3D design platforms, converting digital models into physical prototypes quickly. This allows manufacturers to rapidly test, refine and iterate designs. Integrated workflows lower prototyping costs and improve design-to-production efficiency.
3D design platforms facilitate real-time collaboration among designers, engineers and manufacturers, enhancing alignment and communication. Integrated tools support rapid feedback and adjustments, minimizing errors. This improves decision making, accelerates project timelines, and boosts overall efficiency.
Outsourcing 3D design allows access to specialized skills and advanced tools without straining internal resources. It expedites design iterations, reduces prototyping costs and enhances precision. This allows manufacturers to focus on core operations while improving design quality and speeding up production cycles.
Leave a Reply